模具技術(shù)分享 | Autoform汽車覆蓋件模具全工序沖壓模擬技術(shù)開(kāi)發(fā)與應(yīng)用
2017-04-11 by:CAE仿真在線 來(lái)源:互聯(lián)網(wǎng)
文/唐薇 胡海 東風(fēng)模具沖壓技術(shù)有限公司模具分公司
模具是基礎(chǔ)裝備制造業(yè)的重要組成部分,是制造業(yè)各有關(guān)行業(yè)產(chǎn)業(yè)升級(jí)和技術(shù)進(jìn)步的重要保障之一。隨著時(shí)代的進(jìn)步和科技的發(fā)展,過(guò)去長(zhǎng)期依賴鉗工、以鉗工為核心的粗放型作坊式的生產(chǎn)管理模式,正逐漸被以技術(shù)為依托、以設(shè)計(jì)為中心的集約型現(xiàn)代化生產(chǎn)管理模式所替代。模具制造過(guò)程的前移,使調(diào)試問(wèn)題被提前到加工數(shù)模設(shè)計(jì)乃至沖壓工藝設(shè)計(jì)階段解決,已經(jīng)成為當(dāng)前被廣泛應(yīng)用的模式。
目前,國(guó)際模具領(lǐng)先行業(yè)已廣泛采用CAE 模擬仿真技術(shù),通過(guò)前期的仿真模擬,提高模具設(shè)計(jì)質(zhì)量,減少返工返修時(shí)間,提高裝配、調(diào)試的效率,最終縮短調(diào)試周期,降低調(diào)試成本。其模具設(shè)計(jì)和調(diào)試過(guò)程,已經(jīng)真正形成了一個(gè)閉環(huán)制造系統(tǒng)。
東風(fēng)模具是業(yè)界處于領(lǐng)先地位的模具制造商,率先在國(guó)內(nèi)對(duì)模具全工序沖壓模擬技術(shù)做了系統(tǒng)的、全面的開(kāi)發(fā)與應(yīng)用,從技術(shù)上逐漸縮小與發(fā)達(dá)國(guó)家模具制造水平的差距,更好地滿足國(guó)內(nèi)汽車工業(yè)對(duì)高端覆蓋件模具的需求。
一、總體思路
(1)應(yīng)用虛擬沖壓調(diào)試技術(shù),在沖壓工藝設(shè)計(jì)階段實(shí)現(xiàn)虛擬調(diào)試,提升工藝設(shè)計(jì)水平,縮短調(diào)試周期。
(2)研究基于AUTOFORM 全工序模擬分析(SIM-MP-TB)技術(shù),改進(jìn)現(xiàn)有的SIM 工作流程;建立全工序沖壓模擬及回彈補(bǔ)償?shù)募夹g(shù)標(biāo)準(zhǔn)(評(píng)價(jià)標(biāo)準(zhǔn)、經(jīng)驗(yàn)值、標(biāo)準(zhǔn)作業(yè)書(shū))。
(3)掌握精細(xì)化模面修正技術(shù)(A 級(jí)曲面、間隙和撓度的修正),解決轎車覆蓋件的外觀缺陷。建立外板表面缺陷的判斷基準(zhǔn),建立表面缺陷的歷史經(jīng)驗(yàn)數(shù)據(jù),積累經(jīng)驗(yàn),減少調(diào)試人員的工作量。
二、 主要內(nèi)容及技術(shù)方案
1、全工序成形模擬技術(shù)
目前,東風(fēng)模具使用的AUTOFORM是一款由瑞士開(kāi)發(fā)的專業(yè)薄板成形快速模擬軟件,它采用靜力隱式算法進(jìn)行求解,采用了全拉格朗日理論,由于對(duì)殼單元面內(nèi)和橫向剛度都進(jìn)行了解耦,消除了剛度矩陣的病態(tài),保證了計(jì)算的收斂性,求解速度很快。該軟件可自動(dòng)進(jìn)行網(wǎng)格剖分,自動(dòng)生成和交互修改壓料面、工藝補(bǔ)充部分、拉伸筋、凹模入口線、板坯材料等網(wǎng)格,可以自由選擇調(diào)整沖壓方向,產(chǎn)生工藝切口,模擬重力作用、壓邊、成形、修邊、回彈等全工序或工藝過(guò)程。

圖1 Autoform 全工序成形模擬過(guò)程
在沖壓工藝設(shè)計(jì)中應(yīng)用AUTOFORM軟件仿真模擬,一般分為三個(gè)階段:
第一階段是快速模面設(shè)計(jì)。在沖壓工藝設(shè)計(jì)初期,用CAE軟件中的快速模面設(shè)計(jì)模塊設(shè)計(jì)并調(diào)整拉延工藝補(bǔ)充面,根據(jù)模擬結(jié)果,設(shè)計(jì)者可以很方便地對(duì)工藝補(bǔ)充面進(jìn)行調(diào)整,直到模擬結(jié)果滿足設(shè)計(jì)要求。
在前期工藝設(shè)計(jì)階段能夠改善的工藝參數(shù)有以下幾點(diǎn):
(1)調(diào)整沖壓方向,改善缺陷處的拔模角。
(2)調(diào)整壓料面的高低,以及局部的光順性。
(3)通過(guò)改善工藝補(bǔ)充的型面,來(lái)控制材料的流動(dòng)方向。
(4)通過(guò)改變拉延筋的阻力,來(lái)調(diào)整材料的流入量。
(5)通過(guò)改變板料的形狀,以及增加刺口和切角等手段來(lái)控制材料流入。
(6)通過(guò)改變板料的材料性能,來(lái)解決缺陷問(wèn)題,此方法需要得到產(chǎn)品設(shè)計(jì)人員的認(rèn)可。
第二階段是拉延型面的精細(xì)化仿真模擬。由于快速設(shè)計(jì)是建立在曲面的粗略構(gòu)造上,曲面面片本身以及曲面面片之間的連續(xù)并非十分光順,不能夠直接用于模具表面的加工,但是對(duì)于模擬精度的影響卻不是很大。因此要將第一階段分析構(gòu)造的曲面和Profile 以中性數(shù)據(jù)格式IGS 或VDA輸出,在CAD 軟件中進(jìn)行曲面重構(gòu),得到機(jī)加工可以使用的拉延工序模具數(shù)模并進(jìn)行模擬分析。此階段的模擬分析結(jié)果直接反映出覆蓋件的成形過(guò)程及產(chǎn)生的缺陷。工藝設(shè)計(jì)人員可以根據(jù)模擬分析過(guò)程及結(jié)果,分析缺陷產(chǎn)生的原因,找到解決問(wèn)題的方法。
第三階段是全工序沖壓模擬。這個(gè)階段主要是考證后序翻邊整形工序是否合理,以及判定回彈的量。如果翻邊時(shí)仍產(chǎn)生開(kāi)裂與起皺,則需要重新調(diào)整工藝,同時(shí)對(duì)回彈量進(jìn)行修正補(bǔ)償。
2、回彈與回彈補(bǔ)償技術(shù)
起皺、破裂和回彈是薄板成形中三種主要的質(zhì)量缺陷,其中回彈是最難控制的,因?yàn)樯婕暗交貜椓康臏?zhǔn)確預(yù)測(cè),且不同材料和不同形狀的沖壓件的回彈規(guī)律差別很大。回彈問(wèn)題的存在會(huì)影響沖壓件的形狀尺寸精度和表面質(zhì)量,進(jìn)而影響整車裝配。
東風(fēng)模具從2009 年開(kāi)始采用Think Design GSM 模塊修正沖壓回彈補(bǔ)償。但當(dāng)時(shí)的應(yīng)用處于較低的水平,采用的技術(shù)方案是:根據(jù)調(diào)試模具實(shí)物結(jié)果反饋的尺寸,人工修改回彈造型,然后修改模具。這是一種事后的、基于實(shí)物手工測(cè)量結(jié)果的措施,無(wú)法從根本上解決反復(fù)現(xiàn)場(chǎng)加工調(diào)試的問(wèn)題。
與Think3 廠家多次技術(shù)交流和對(duì)需求的了解,針對(duì)東風(fēng)模具的實(shí)際需求,提出相應(yīng)的沖壓件鈑金回彈處理系統(tǒng):TD Compensator,實(shí)現(xiàn)回彈補(bǔ)償過(guò)程的自動(dòng)化。此系統(tǒng)能夠在保持原有曲面的質(zhì)量上對(duì)模具型面進(jìn)行修改,修改后的型面保持和原先型面相同的曲面拓補(bǔ)結(jié)構(gòu)和曲面質(zhì)量。該系統(tǒng)通過(guò)AUTOFORM 進(jìn)行全工序模擬分析,利用Think Design 模塊讀取模擬分析MESH 結(jié)果,自動(dòng)進(jìn)行回彈補(bǔ)償模面設(shè)計(jì),獲得最佳曲面質(zhì)量,節(jié)省MP 設(shè)計(jì)時(shí)間40% ~ 80%,實(shí)現(xiàn)把回彈補(bǔ)償數(shù)據(jù)加入到NC 加工數(shù)據(jù)中,在模具調(diào)試前對(duì)回彈進(jìn)行預(yù)測(cè)和補(bǔ)償,減少車間的反復(fù)加工、調(diào)試修改。
實(shí)施本項(xiàng)目的關(guān)鍵是:
(1)所有零件實(shí)施了全工序模擬。
(2)采購(gòu)Think3 的回彈補(bǔ)償模面設(shè)計(jì)模塊(讀取AUTOFORM MESH 數(shù)據(jù)的方式)。
(3)研究基于AUTOFORM 全工序模擬分析(SIM-MP-TB)技術(shù),改進(jìn)現(xiàn)有的SIM 工作流程。
(4)建立全工序沖壓模擬及回彈補(bǔ)償?shù)募夹g(shù)標(biāo)準(zhǔn)(評(píng)價(jià)標(biāo)準(zhǔn)、經(jīng)驗(yàn)值、標(biāo)準(zhǔn)作業(yè)書(shū))。
(5)制定本技術(shù)的長(zhǎng)期發(fā)展計(jì)劃(從內(nèi)表件到外表件,從薄板到厚板和高強(qiáng)度板,從MESH 數(shù)據(jù)到掃描點(diǎn)云數(shù)據(jù))。
3、 外板件表面缺陷的CAE 預(yù)測(cè)
一直以來(lái),我們認(rèn)為凹陷、滑移與產(chǎn)品設(shè)計(jì)方案相關(guān),很難從工藝設(shè)計(jì)、調(diào)試的角度解決,沒(méi)有采取有效的技術(shù)措施,一旦發(fā)生缺陷,往往依賴現(xiàn)場(chǎng)調(diào)試減輕缺陷,而顧客默認(rèn)接受缺陷。
為了解決上述問(wèn)題,近年來(lái),東風(fēng)模具運(yùn)用AUTOFORM 模擬分析技術(shù),在門外板、頂蓋等零件上開(kāi)展了A 面修正技術(shù)的嘗試( 見(jiàn)圖2)。以零件為單位,制定零件凹陷部位圖表,通過(guò)對(duì)凹陷實(shí)際數(shù)據(jù)的測(cè)量,制定“凹陷過(guò)隆”補(bǔ)償標(biāo)準(zhǔn)和“強(qiáng)壓”間隙標(biāo)準(zhǔn);制定“過(guò)隆”補(bǔ)償研磨標(biāo)準(zhǔn)作業(yè)書(shū)。用未修正的數(shù)據(jù)做模擬分析找到A面塌陷結(jié)果,確定拉延模A 面修正方案。
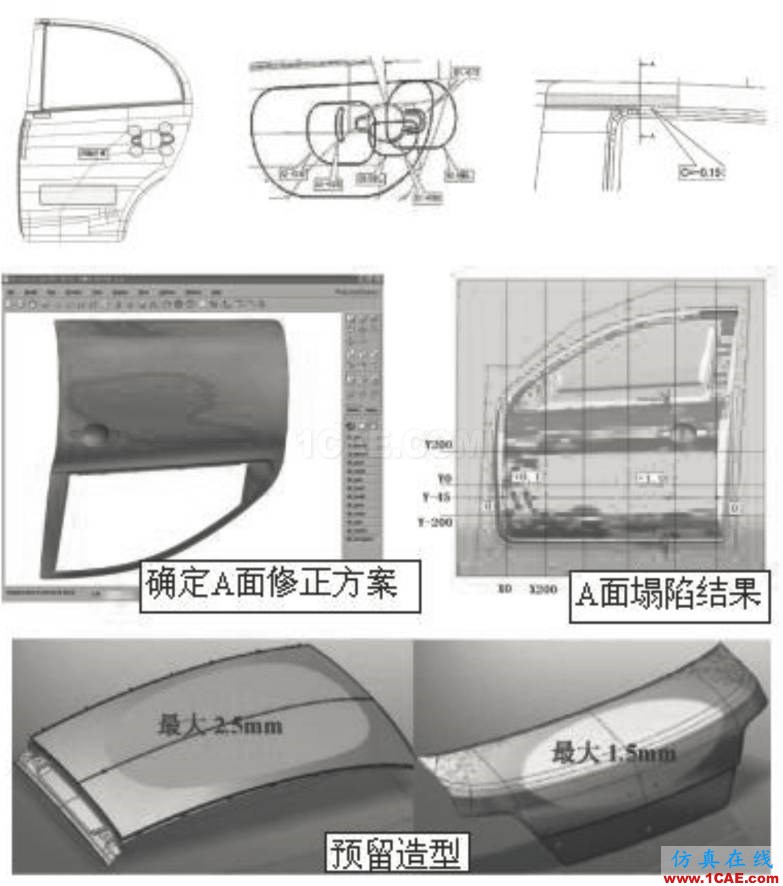
圖2 修正技術(shù)的嘗試
4. 建立沖壓模擬分析標(biāo)準(zhǔn)
(1)為了規(guī)范AUTOFORM 軟件的使用操作,避免由于軟件參數(shù)設(shè)置不正確導(dǎo)致的運(yùn)算結(jié)果不一致的情況,我們結(jié)合公司的實(shí)際情況,完成了《AUTOFORM 軟件使用指令標(biāo)準(zhǔn)作業(yè)書(shū)》、《AUTOFORM軟件操作說(shuō)明書(shū)》及《CAE 文件的命名規(guī)范》的編寫。
(2) 為了完善CAE, 建立了《CAE分析檢查表》和《CAE分析典型件常見(jiàn)不良案例》。
(3)制定《CAE 成型品質(zhì)保證單及調(diào)試跟蹤記錄卡》,跟蹤對(duì)比CAE 模擬與車間調(diào)試的符合率情況。
(4) 制定合理的CAE 判斷標(biāo)準(zhǔn)及SIM 分析風(fēng)險(xiǎn)(V1V2V3)評(píng)價(jià)標(biāo)準(zhǔn),對(duì)起皺、變薄、板料厚度、滑移線、表面缺陷等指標(biāo)作出量化規(guī)定。
(5)CAE 模擬分析材料庫(kù)參數(shù)的修訂和調(diào)試板料驗(yàn)證。
三、應(yīng)用情況實(shí)例
1、D23 項(xiàng)目側(cè)圍零件
圖3 為D23 側(cè)圍案例,由于在模擬階段忽略了后工序的模擬,后序翻邊的現(xiàn)場(chǎng)調(diào)試時(shí)由于多料而出現(xiàn)起皺疊料,我們通過(guò)CAE 驗(yàn)證分析,得到了與現(xiàn)場(chǎng)調(diào)試一樣的結(jié)果。通過(guò)修改OP40 的整形形狀,改善了此處的起皺問(wèn)題。
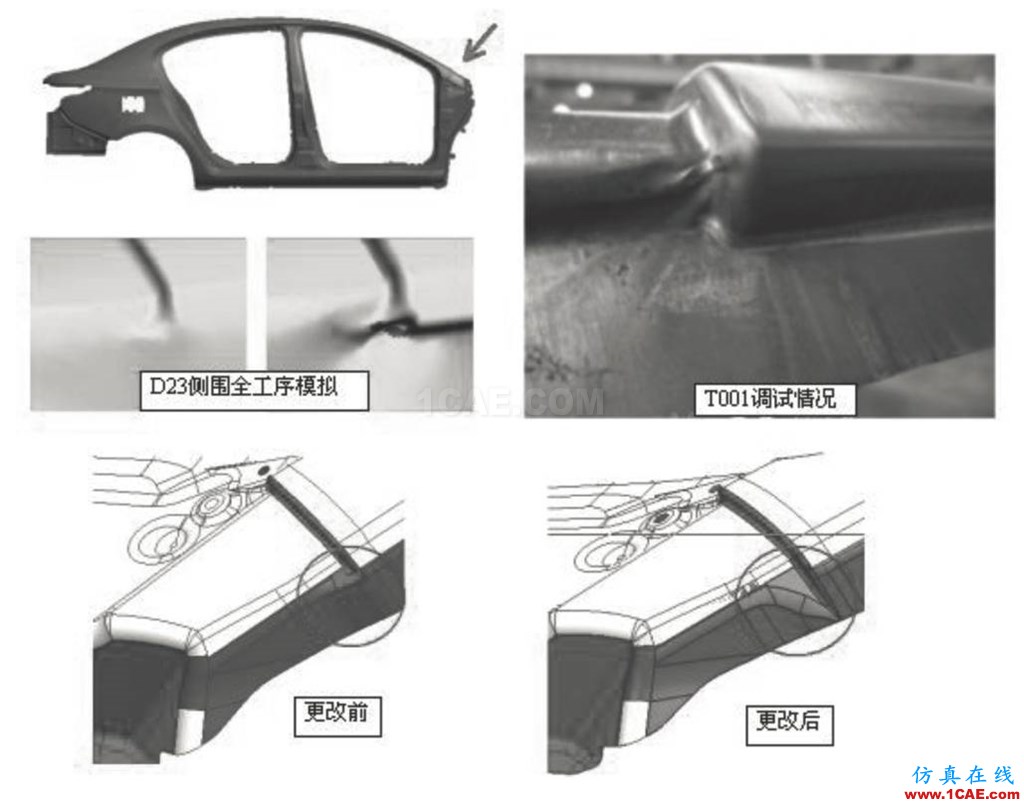
圖3 CAE 分析示例1
2. Z982 項(xiàng)目側(cè)圍零件
圖4 為Z982 側(cè)圍零件案例。
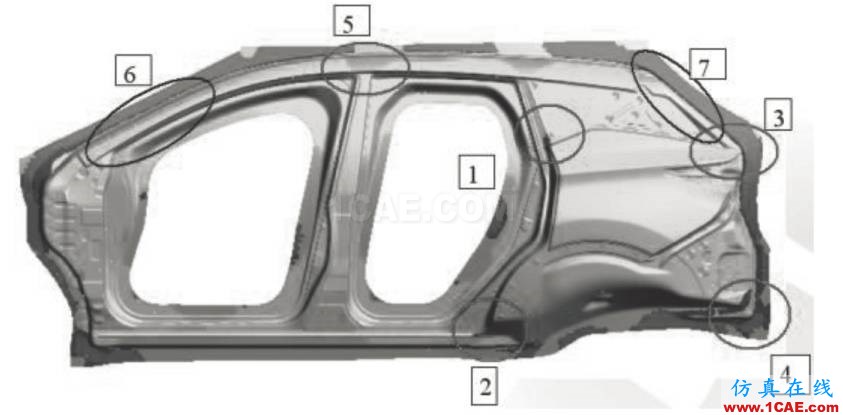
圖4 CAE 分析示例2
(1)CAE 分析有開(kāi)裂起皺風(fēng)險(xiǎn),現(xiàn)場(chǎng)調(diào)試與CAE 一致,加筋,但未徹底解決問(wèn)題(見(jiàn)圖5)。
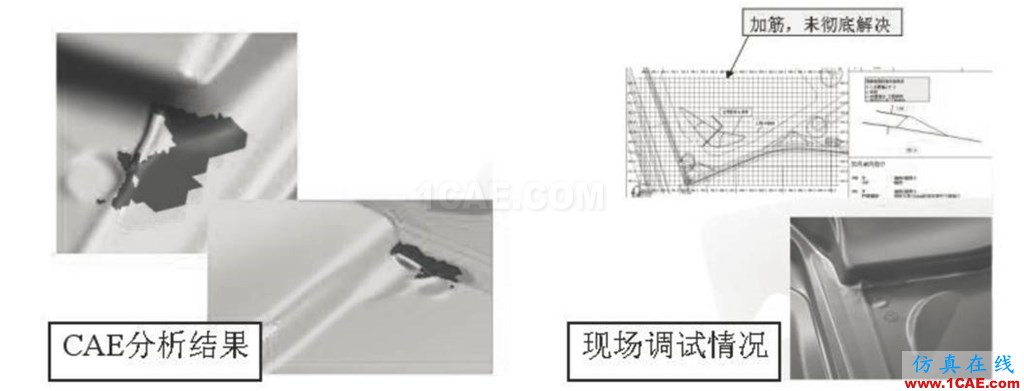
圖5
(2)CAE 分析有起皺風(fēng)險(xiǎn),現(xiàn)場(chǎng)調(diào)試與CAE 一致,改筋,增加阻力(見(jiàn)圖6)。
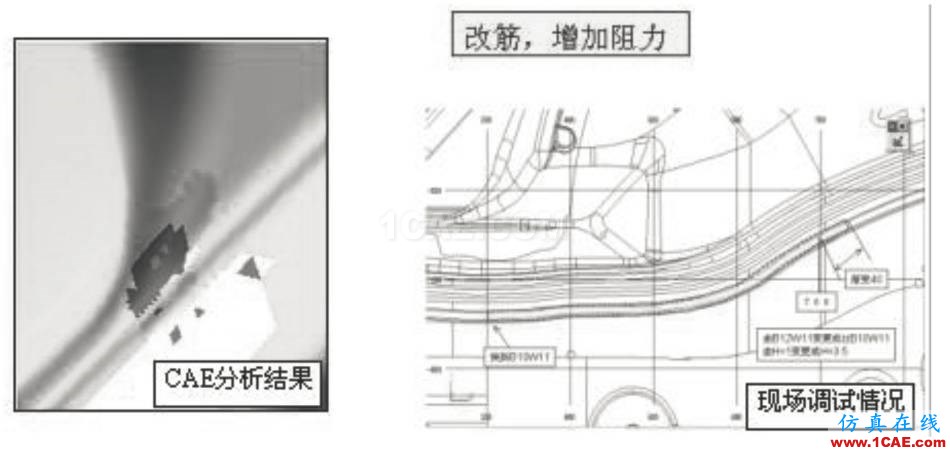
圖6
(3)CAE 分析有起皺風(fēng)險(xiǎn),現(xiàn)場(chǎng)調(diào)試與CAE 模擬一致,沒(méi)有對(duì)策。
(4)下死點(diǎn)5mm 處時(shí)有起皺風(fēng)險(xiǎn),調(diào)試時(shí)拉延模此處有皺,產(chǎn)品此處有皺( 見(jiàn)圖7)。
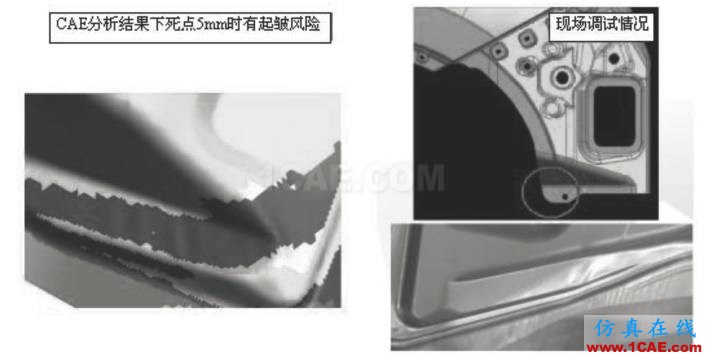
圖7
(5)CAE 分析6、7 處有滑移,通過(guò)外壓料圈降筋增加流入量解決( 見(jiàn)圖8)。
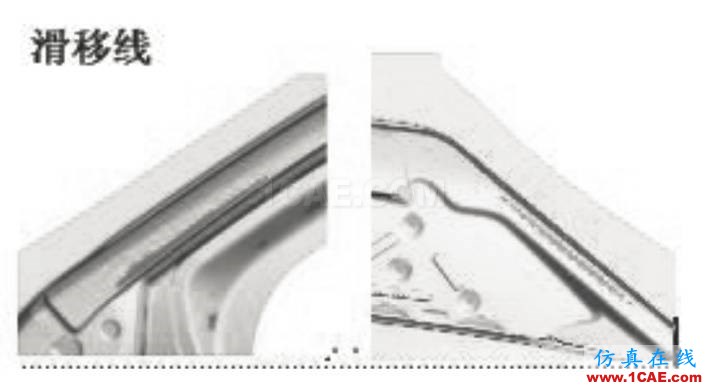
圖8
3. 門外板凹陷預(yù)測(cè)及改善對(duì)策
CAE 模擬結(jié)果三處有凹陷——V1 缺陷,對(duì)策是參考CAE 分析結(jié)果,結(jié)合現(xiàn)場(chǎng)調(diào)試數(shù)據(jù),根據(jù)零件類型制定TB 補(bǔ)償方案( 見(jiàn)圖9)。
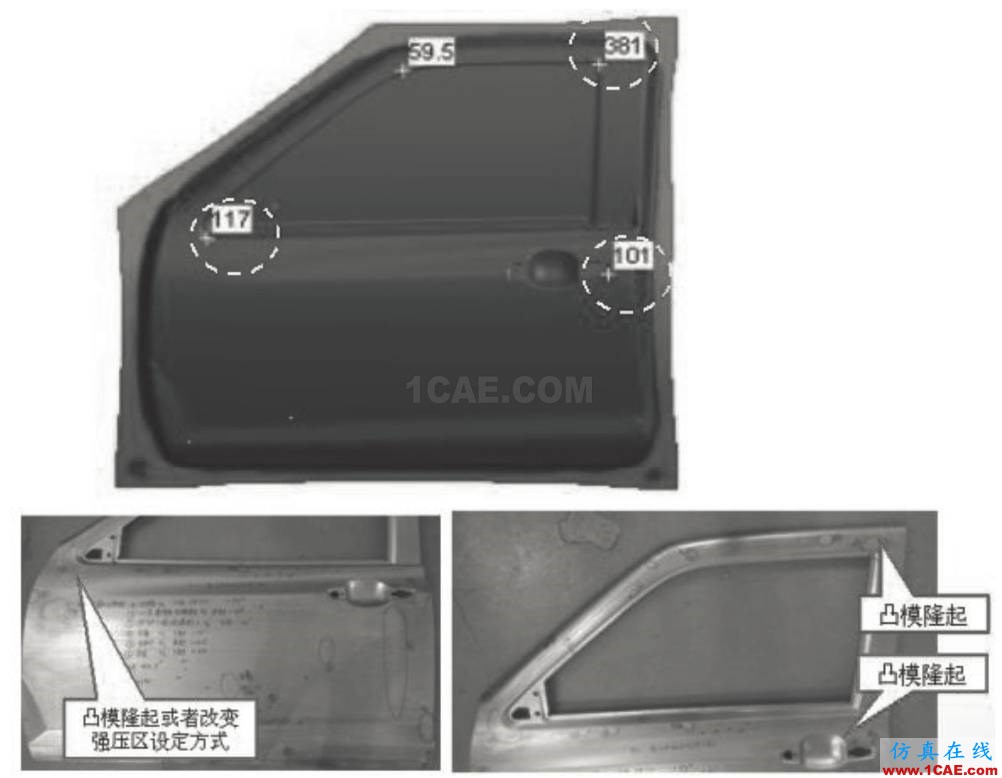
圖9 凹陷預(yù)測(cè)及改善案例
4. 左/ 右前縱梁下加強(qiáng)板進(jìn)行全工序模擬后回彈補(bǔ)償
圖10 是我們對(duì)左/ 右前縱梁下加強(qiáng)板進(jìn)行全工序模擬后回彈補(bǔ)償?shù)陌咐?
采用AUTOFORM 分析,提供原始數(shù)模、原始網(wǎng)格和成型網(wǎng)格,導(dǎo)入Think Design Compensator 自動(dòng)回彈補(bǔ)償修改時(shí)間:32min(其中條件設(shè)定:25min,回彈計(jì)算:7min),整改回彈的過(guò)程需30min。
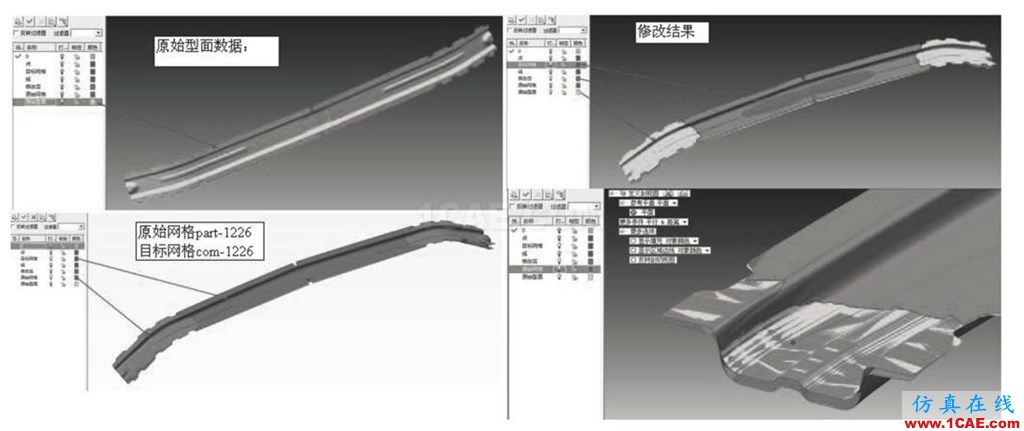
圖10 左/ 右前縱梁下加強(qiáng)板回彈補(bǔ)償案例
效益評(píng)估:
(1)曲面連續(xù)性可達(dá)到G2 連續(xù),達(dá)到A 級(jí)曲面要求,保證了原有曲面的拓?fù)潢P(guān)系和曲面數(shù)量。
(2)之前處理類似工件需要3 ~4h,現(xiàn)在的設(shè)計(jì)時(shí)間可以節(jié)省65% ~ 79%,效率提高了2 ~ 4 倍。
(3)減少了反復(fù)修改的重復(fù)勞動(dòng)。
四、效益分析
通過(guò)CAE 技術(shù)的應(yīng)用,縮短了調(diào)試周期40% ~ 50%。更重要的是,汽車覆蓋件的質(zhì)量得到了大大的提高,其意義超過(guò)了縮短制造周期本身。
自動(dòng)進(jìn)行回彈補(bǔ)償模面設(shè)計(jì),獲得最佳曲面質(zhì)量,節(jié)省MP設(shè)計(jì)時(shí)間65% ~ 79%,效率提高2 ~ 4 倍。實(shí)現(xiàn)了把回彈補(bǔ)償數(shù)據(jù)加入到NC 加工數(shù)據(jù)中,在模具調(diào)試前對(duì)回彈進(jìn)行預(yù)測(cè)和補(bǔ)償,減少車間的反復(fù)加工、調(diào)試和修改。不良率得到降低,保守估計(jì)在5% 以上,部分項(xiàng)目可減少試模1 ~ 2次,節(jié)省了直接成本。
該項(xiàng)目成功應(yīng)用于轎車覆蓋件模具的開(kāi)發(fā)和制造,通過(guò)全工序模擬,提前預(yù)測(cè)和解決模具調(diào)試階段可能出現(xiàn)的各類缺陷,縮短了模具制造周期,提高了零件品質(zhì),具有良好的經(jīng)濟(jì)效益。
五、總結(jié)與展望
東風(fēng)模具率先在國(guó)內(nèi)針對(duì)模具設(shè)計(jì)模擬技術(shù)進(jìn)行了系統(tǒng)性的研究,并開(kāi)發(fā)了一整套模具設(shè)計(jì)模擬的技術(shù)規(guī)范和流程,成功地應(yīng)用于公司各個(gè)項(xiàng)目的模具設(shè)計(jì)和模具制造,使得模具設(shè)計(jì)質(zhì)量得以提高,制造周期有效縮短,鉗工、調(diào)試人員的勞動(dòng)強(qiáng)度明顯降低,東風(fēng)模具的設(shè)計(jì)能力、制造能力和模具品質(zhì)得到顯著提升,產(chǎn)生了巨大的社會(huì)效益,在國(guó)內(nèi)汽車模具行業(yè)具有極強(qiáng)的推廣應(yīng)用價(jià)值。
(內(nèi)容來(lái)源:“《中國(guó)模具信息》雜志”)
相關(guān)標(biāo)簽搜索:模具技術(shù)分享 | Autoform汽車覆蓋件模具全工序沖壓模擬技術(shù)開(kāi)發(fā)與應(yīng)用 Autoform分析培訓(xùn)班 Autoform汽車模具仿真 Autoform視頻教程 Autoform資料下載 在線軟件培訓(xùn) 汽車鈑金代做 Fluent、CFX流體分析 HFSS電磁分析 Ansys培訓(xùn) Abaqus培訓(xùn) 有限元培訓(xùn) Solidworks培訓(xùn)