高強(qiáng)鋼的成形方法及應(yīng)用
2016-09-26 by:CAE仿真在線 來源:互聯(lián)網(wǎng)
(作者:尤 超 文章來源:瑞典SSAB鋼板有限公司)
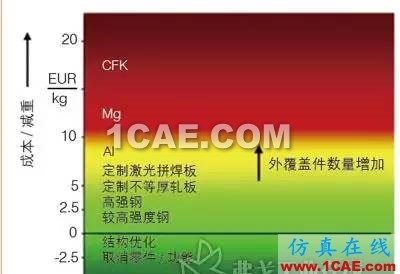
與鋁合金及鎂合金相比,先進(jìn)高強(qiáng)鋼因其成本低而具有很強(qiáng)的市場(chǎng)競(jìng)爭(zhēng)力,在汽車輕量化、提高安全性及節(jié)能減排等方面,都展現(xiàn)出了廣闊的應(yīng)用前景。然而,在先進(jìn)高強(qiáng)鋼的應(yīng)用過程中,減薄和高強(qiáng)兩大優(yōu)勢(shì)卻對(duì)成形工藝提出了新的挑戰(zhàn)。本文簡(jiǎn)述了先進(jìn)高強(qiáng)鋼的三種常用成形方法。
節(jié)能、安全和環(huán)保是當(dāng)今世界汽車發(fā)展的主題。據(jù)分析,減少汽車自重是降低汽車燃油消耗及減少排放的有效措施之一。由于鋼鐵材料在強(qiáng)度、塑性、抗沖擊能力、回收使用及低成本方面具有綜合的優(yōu)越性,其在汽車材料中的主導(dǎo)地位仍是不可動(dòng)搖的。隨著先進(jìn)高強(qiáng)鋼 (AHSS) 在汽車制造中的比例不斷增大,廣泛應(yīng)用于汽車車身、底盤、懸架和轉(zhuǎn)向等零部件上,用高強(qiáng)度鋼板代替普通的低碳冷軋鋼板、鋁合金和鎂合金等已成為未來的主要發(fā)展方向之一。
圖1所示為德國(guó)寶馬汽車公司的研究成果:以先進(jìn)高強(qiáng)鋼為基準(zhǔn),每減重1kg時(shí)各種材料、工藝等所帶來的成本變化。其中,用鋁每減重1kg,成本增加7.5歐元左右;用鎂每減重1kg,成本增加12.5歐元左右。
先進(jìn)高強(qiáng)鋼的定義
先進(jìn)高強(qiáng)鋼具有優(yōu)良的材料性能,由于迎合了超輕鋼車身先進(jìn)車輛概念(ULSAB-AVC)的安全、節(jié)能和經(jīng)濟(jì)的先進(jìn)理念,先進(jìn)高強(qiáng)鋼在汽車工業(yè)輕量化中得到了日益廣泛的應(yīng)用。目前,市場(chǎng)上的先進(jìn)高強(qiáng)鋼主要有雙相鋼(DP)、復(fù)相鋼(CP)、相變誘發(fā)塑性鋼(TRIP)和馬氏體鋼(MART)等(見圖2),強(qiáng)度范圍為500~1600MPa。其中,雙相鋼和馬氏體鋼是目前市場(chǎng)上應(yīng)用最廣泛的先進(jìn)高強(qiáng)鋼,瑞典SSAB公司生產(chǎn)DOCOL1500M是目前市場(chǎng)強(qiáng)度最高的冷軋馬氏體鋼。
先進(jìn)高強(qiáng)鋼的成形方法
目前常用的先進(jìn)高強(qiáng)鋼的成形方法主要有:輥壓成形、冷沖壓成形和熱沖壓成形。
1.輥壓成形工藝
輥壓成形(又稱滾壓成形)工藝是通過順序配置的多道次成形軋輥,把卷材、帶材等金屬板帶不斷地進(jìn)行橫向彎曲,以制成特定斷面的型材。
輥壓成形工藝具有以下優(yōu)點(diǎn):
(1)最高可生產(chǎn)強(qiáng)度為1500MPa的零件,如某前碰撞橫梁(見圖3)采用DOCOL1500M(抗拉強(qiáng)度1500MPa)替代DOCOL1200M(抗拉強(qiáng)度1200MPa),輥壓成形后板厚減少0.2mm,質(zhì)量降低0.75kg。
(2)生產(chǎn)效率高,適合于大批量生產(chǎn),與沖壓工藝相比效率提高10倍以上,制造成本大幅降低;
(3)加工產(chǎn)品的長(zhǎng)度基本不受限制,可實(shí)現(xiàn)不同車型同一零件的模塊化設(shè)計(jì),降低制造成本,如某品牌3款不同車型車門檻板(見圖4)設(shè)計(jì)為同一截面,材料牌號(hào):DOCOL1000DP,抗拉強(qiáng)度:1000MPa,3款車型共用同一生產(chǎn)線,實(shí)現(xiàn)了生產(chǎn)線共用;
(4)能有效解決超高強(qiáng)度鋼的回彈現(xiàn)象,可達(dá)到極小成形半徑;
(5)不需專用成形模具;
(6)產(chǎn)品的表面質(zhì)量好,尺寸精度高;
(7)在輥壓成形生產(chǎn)線上可以集成其他的加工工藝,如沖孔、焊接及壓花等。如某輥壓成形的車門檻板(見圖5),材料牌號(hào):DOCOL1400M,抗拉強(qiáng)度:1400MPa,沖孔在輥壓過程中完成;
(8)材料利用率高,一般可達(dá)到90%以上;
(9)生產(chǎn)噪聲低,無環(huán)境污染。
輥壓成形工藝加工出來的型材其斷面結(jié)構(gòu)合理、幾何尺寸精確,體現(xiàn)了現(xiàn)代社會(huì)對(duì)材料輕量化、合理化及功能化的使用要求。輥壓成形采用先進(jìn)的高效生產(chǎn)工藝,使成形截面達(dá)到最好的力學(xué)性能,特別適用于超高強(qiáng)度鋼零件的加工成形,其有效地解決了超高強(qiáng)度鋼的回彈,并極大地降低了制造成本,推進(jìn)了超高強(qiáng)度鋼在汽車工業(yè)中的應(yīng)用。采用該工藝加工的典型零件有汽車前后碰撞橫梁、車門檻板和座椅滑軌等。
輥壓成形工藝的不足之處在于要求所加工零件截面為等截面,對(duì)零件設(shè)計(jì)提出了更高的要求。
2.冷沖壓成形
冷沖壓成形是用壓力機(jī)通過模具將料板冷沖壓成形產(chǎn)品,主要步驟有拉延成形、切邊和整形等。
冷沖壓成形工藝具有以下優(yōu)點(diǎn):
(1) 最高可生產(chǎn)強(qiáng)度為1400MPa的零件;
(2) 生產(chǎn)線成本不高,普通零件如車門防撞梁用800t的液壓機(jī)或機(jī)械壓力機(jī)即能滿足生產(chǎn)要求;
(3) 零件生產(chǎn)效率比較高;
(4)可以使用AUTOFORM、DYNAFORM等軟件進(jìn)行成形模擬分析。
其不足之處在于:
(1)材料利用率不高,根據(jù)零件形狀、模具設(shè)計(jì)等不同,一般為40%~75%;
(2)產(chǎn)品回彈、褶皺和壁翹曲難以控制,模具調(diào)試時(shí)間長(zhǎng);
(3)模具設(shè)計(jì)和加工復(fù)雜;
(4)生產(chǎn)過程中噪聲大,特別是切邊工序;
(5)太過于復(fù)雜的零件成形困難,需要多步成形,成本增加,如汽車B柱。
高強(qiáng)度鋼的冷沖壓件在生產(chǎn)時(shí),遇到的最大難題是成形件尺寸精度難以保證。為了解決這一難題,需要用AUTOFORM等軟件進(jìn)行成形模擬分析,并多次調(diào)模以減少回彈及壁翹曲。但對(duì)于一些非等截面零件,因?yàn)椴荒懿捎幂亯撼尚?而冷沖壓成形相對(duì)于熱沖壓成形生產(chǎn)成本低,所以也廣泛應(yīng)用于汽車零部件的制造中。其中最典型的零件如:車門防撞桿、底板縱橫梁和車頂縱橫梁等。如圖6所示,冷沖壓成形的車門防撞梁,材料牌號(hào):DOCOL1200M,替代熱成形零件。
3.熱沖壓成形
熱沖壓成形工藝過程首先把常溫下強(qiáng)度為500~600MPa的高強(qiáng)度硼合金鋼板(俗稱硼鋼,如20MnB5、22MnB5和30 MnB5等) 加熱到900~950℃并保持5~10min,使之均勻奧氏體化,然后送入內(nèi)部帶有冷卻系統(tǒng)的模具內(nèi)熱沖壓成形,之后保壓快速冷卻淬火(冷卻速度> 50℃/s),使奧氏體轉(zhuǎn)變成馬氏體。成形件因而得到強(qiáng)化硬化,屈服強(qiáng)度可以達(dá)到1000MPa以上,抗拉強(qiáng)度可以達(dá)到1500MPa以上。
高強(qiáng)度鋼板的熱沖壓成形工藝的基本流程是:落料—預(yù)成形—加熱—沖壓成形—去氧化皮—激光切邊沖孔—防銹處理,并在沖壓成形和保壓定形階段同時(shí)進(jìn)行板件淬火。圖7所示為熱沖壓成形的工藝流程。
這項(xiàng)工藝的核心內(nèi)容在于其沖壓成形中的保壓定型過程以及模具的冷卻。其優(yōu)點(diǎn)是:
(1)最高可生產(chǎn)強(qiáng)度為1500MPa的零件;
(2)高溫下材料塑性好,成形能力強(qiáng),可成形比較復(fù)雜的零件,如汽車B柱;
(3)高溫下成形沒有回彈,成形極限高,實(shí)現(xiàn)高精度成形,成形后零件強(qiáng)度等性能指標(biāo)大幅度提高。
不足之處在于:
(1)生產(chǎn)線復(fù)雜,設(shè)備投資大;
(2)生產(chǎn)、維護(hù)和保養(yǎng)復(fù)雜,生產(chǎn)成本高;
(3)模具設(shè)計(jì)和加工復(fù)雜;
(4)生產(chǎn)節(jié)拍慢;
(5)零件強(qiáng)度容易受到生產(chǎn)零件的影響而產(chǎn)生波動(dòng),生產(chǎn)過程控制要求極為嚴(yán)格。
熱沖壓成形技術(shù)因?yàn)槠漭^強(qiáng)的成形能力仍然在汽車工業(yè)中有著廣泛的應(yīng)用,其中最典型的零件如汽車B柱(見圖8),材料牌號(hào):20MnB5;板厚:1.85mm;成形后抗拉強(qiáng)度:1500MPa。
高強(qiáng)鋼板成形技術(shù)發(fā)展趨勢(shì)
盡管高強(qiáng)鋼板成形技術(shù)的研究已取得了長(zhǎng)足的進(jìn)步,但由于高強(qiáng)鋼板成形性能的特殊性及復(fù)雜性,還需要不斷地進(jìn)行技術(shù)創(chuàng)新。在此,簡(jiǎn)單介紹一些高強(qiáng)鋼成形方面的最新研究。
1.不等厚板熱成形技術(shù)
該技術(shù)可以實(shí)現(xiàn)不同部位不同強(qiáng)度、不同厚度及不同材質(zhì),主要優(yōu)點(diǎn)有:大大減輕車身重量;減少汽車零部件的數(shù)量,因而減少了模具數(shù)量;提高了材料利用率,廢料大大減少;結(jié)構(gòu)功能與工藝性能得到提高。
2. 柔性輥壓成形技術(shù)
與傳統(tǒng)等截面輥壓成形相比,變截面柔性輥壓成形是成形截面沿縱向變化的,因而具有更合理的力學(xué)性能,結(jié)合材料的使用技術(shù),對(duì)超高強(qiáng)度材料零部件進(jìn)行成形加工,整車質(zhì)量可進(jìn)一步降低25%,將成為下一代輥壓成形技術(shù)的發(fā)展方向。國(guó)內(nèi)外,如德國(guó)達(dá)姆施塔特大學(xué)(見圖9)、我國(guó)北方工業(yè)大學(xué)(見圖10)等在柔性輥壓成形方面都頗有研究。
結(jié)語
汽車輕量化是大勢(shì)所趨,而采用先進(jìn)高強(qiáng)鋼是實(shí)現(xiàn)輕量化的主要技術(shù)途徑之一。同時(shí),制造工藝的改進(jìn)和成形技術(shù)的發(fā)展,也促進(jìn)了先進(jìn)高強(qiáng)鋼在汽車制造領(lǐng)域的應(yīng)用。目前市場(chǎng)上最常用的先進(jìn)高強(qiáng)鋼的成形方法主要有:輥壓成形、冷沖壓成形和熱沖壓成形。而就制造成本而言,輥壓成形最優(yōu),冷沖壓成形次之,熱沖壓成形成本最高。
我國(guó)汽車輕量化起步較晚,相關(guān)高強(qiáng)鋼成形工藝技術(shù)與國(guó)外有著一定的差距。但我國(guó)高校、科研院所、汽車及零部件廠家正積極努力,致力于提高自身的設(shè)計(jì)能力和制造工藝水平,為加速我國(guó)汽車輕量化的步伐,為節(jié)能環(huán)保做出了一定的貢獻(xiàn)。
相關(guān)標(biāo)簽搜索:高強(qiáng)鋼的成形方法及應(yīng)用 Autoform分析培訓(xùn)班 Autoform汽車模具仿真 Autoform視頻教程 Autoform資料下載 在線軟件培訓(xùn) 汽車鈑金代做 Fluent、CFX流體分析 HFSS電磁分析 Ansys培訓(xùn) Abaqus培訓(xùn) 有限元培訓(xùn) Solidworks培訓(xùn)